
Switch the digital genius on
Be productive with Twiserion Fleet Manager
Twiserion Fleet Manager provides comprehensive fleet management, as well as the fleet’s real-time monitoring and display of the current status and the performed request. Thanks to the collected statistical data, the customer can easily identify problem areas and focus on their optimization.
Twiserion Fleet Manager
Twiserion Fleet Manager consists of three main components, namely the Control System, the Monitoring System (AGV Monitor), and the Track & Trace System.
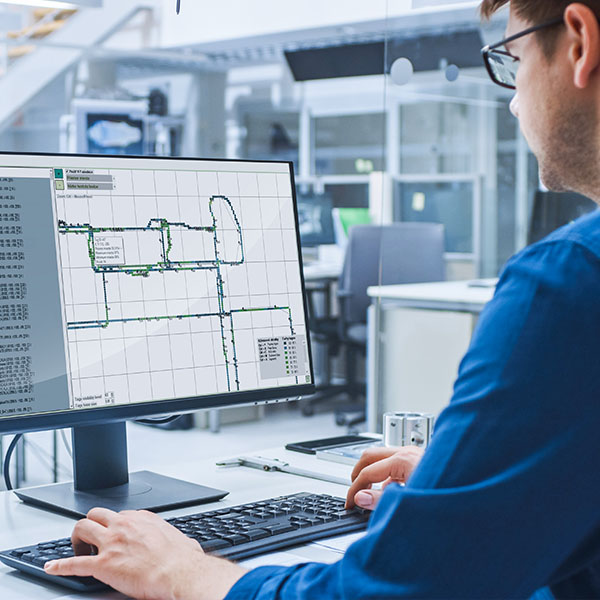
Control System
The Control System is the control unit that serves as the basis for the whole system that provides autonomous AGVs with the transmission of information about its status, performed activities, problem situations, and positions within the defined area, while using this information for decision-making and the subsequent management of individual parts of the logistics process of these resources.
The Control System is used to manage the logistics devices active in the production process. Its task is to control the transfer of individual AGV robots, e.g. through intersections, traffic lights, service points, chargers and the like, automatically without the need for human intervention. The added value of the Control System is the automatic management and control of the logistics process.

AGV Monitor
Asseco CEIT’s AGV Monitor oversees autonomous AGVs and other system elements active in the manufacturing process. The role of the AGV Monitor is to offer employees in the industrial hall the opportunity to monitor the position, activity, operating status of individual mobile robots and other system elements, and to have an overall overview and control over them in real time.
The added value of the AGV Monitor is the real-time monitoring of AGVs in the production process, while the processed information is displayed in a user-friendly form, especially by graphical visualization or in a user-adjustable output of status information in text form. The user has the possibility to influence individual elements in real time, for example by activation or deactivation. All information, actions or changes in settings are recorded and collected by the system as a basis for later analysis or subsequent optimization of logistics processes.
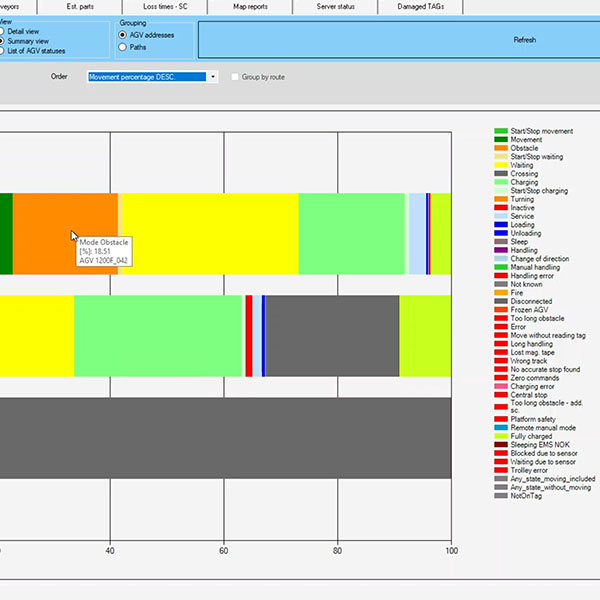
Track & Trace Statistical Software
Track & Trace is provides an insight into the history of production and logistics processes implemented in the industrial halls of various industries. The software records, statistically evaluates and displays the operational activities of individual autonomous mobile robots, provides a regular report on their overall movement, material transhipment, communication response, correct reading of RFID tags, etc.
With the help of Track & Trace, it is possible to find out the operating status and occupancy status of peripherals located in the industrial hall, their reloading of materials, monitor the movement of individual pallets around the industrial hall (material flow), etc. Based on the statistics provided by Track & Trace, bottlenecks may be identified and the unreliability of technology or the human factor, can be eliminated together with failures and causes of problems. Such analyses are an asset to optimization of the production and logistics processes in industrial companies. The software provides feedback for the production and logistics processes, thus providing a comprehensive overview of the overall situation in the industrial hall.
Advantages of the Control System
![]() |
✔ |
Smart control |
✔ |
Possibility to evaluate the conditions of transport and decide on the basis of them |
|
✔ |
Automatically generated input information for transport from various external devices (e.g. robotic workstations, production/assembly line, external devices and customer systems) automatically sent to the control system |
|
✔ |
Sending information from the AGV to other external devices |
|
✔ |
Synchronization with just-in-time and on-demand manufacturing |
|
✔ |
Acceleration and continuity of material flow |
|
✔ |
Full automation of production/logistics process |
Advantages of AGV Monitor
![]() |
✔ | Monitoring of the position, operation and operating status of autonomous AGV equipment and other system elements (peripherals, traffic lights, etc.) |
✔ | Monitoring of the status of requests sent from an external system (e.g. from the customer’s internal system) | |
✔ | Real-time graphical visualization of collected data in a user-friendly form | |
✔ | Ability to monitor the duration of individual operating conditions over time | |
✔ | Ability to monitor the presence/absence of the AGV at a specific location in real time and thus urge, for example, the operator in a workplace | |
✔ | Possibility to inform about defective/faulty material, which AGV carries or the static conveyor contains | |
✔ | Error notification and abnormal situations are immediately displayed on the warning panel | |
✔ | Possibility to display the occupancy of intersections |
Advantages of Track & Trace
![]() |
✔ |
Collection, storage and evaluation of historical data and their graphical visualization for production and logistics managers |
✔ |
Recording of historical data from the production process to identify bottlenecks in the logistics process |
|
✔ |
A tool providing regular feedback on operational activities carried out in industrial halls |
|
✔ |
Activity statistics and utilization monitoring the autonomous AGV equipment |
|
✔ |
Statistics on the operating conditions and occupancy status of the AGV tractor’s peripherals |
|
✔ |
Graphical display of historical data related, for example, to specific AGV status information, distance travelled, errors, network response, number of parts produced, the functionality of the server and its components in user-defined time intervals |
Advantages of the Control System
✔ | Smart control |
✔ | Possibility to evaluate the conditions of transport and decide on the basis of them |
✔ | Automatically generated input information for transport from various external devices (e.g. robotic workstations, production/assembly line, external devices and customer systems) automatically sent to the control system |
✔ | Sending information from the AGV to other external devices |
✔ | Synchronization with just-in-time and on-demand manufacturing |
✔ | Acceleration and continuity of material flow |
✔ | Full automation of production/logistics process |
Advantages of AGV Monitor
✔ | Monitoring of the position, operation and operating status of autonomous AGV equipment and other system elements (peripherals, traffic lights, etc.) |
✔ | Monitoring of the status of requests sent from an external system (e.g. from the customer’s internal system) |
✔ | Real-time graphical visualization of collected data in a user-friendly form |
✔ | Ability to monitor the duration of individual operating conditions over time |
✔ | Ability to monitor the presence/absence of the AGV at a specific location in real time and thus urge, for example, the operator in a workplace |
✔ | Possibility to inform about defective/faulty material, which AGV carries or the static conveyor contains |
✔ | Error notification and abnormal situations are immediately displayed on the warning panel |
✔ | Possibility to display the occupancy of intersections |
Advantages of Track & Trace
✔ | Collection, storage and evaluation of historical data and their graphical visualization for production and logistics managers |
✔ | Recording of historical data from the production process to identify bottlenecks in the logistics process |
✔ | A tool providing regular feedback on operational activities carried out in industrial halls |
✔ | Activity statistics and utilization monitoring the autonomous AGV equipment |
✔ | Statistics on the operating conditions and occupancy status of the AGV tractor’s peripherals |
✔ | Graphical display of historical data related, for example, to specific AGV status information, distance travelled, errors, network response, number of parts produced, the functionality of the server and its components in user-defined time intervals |